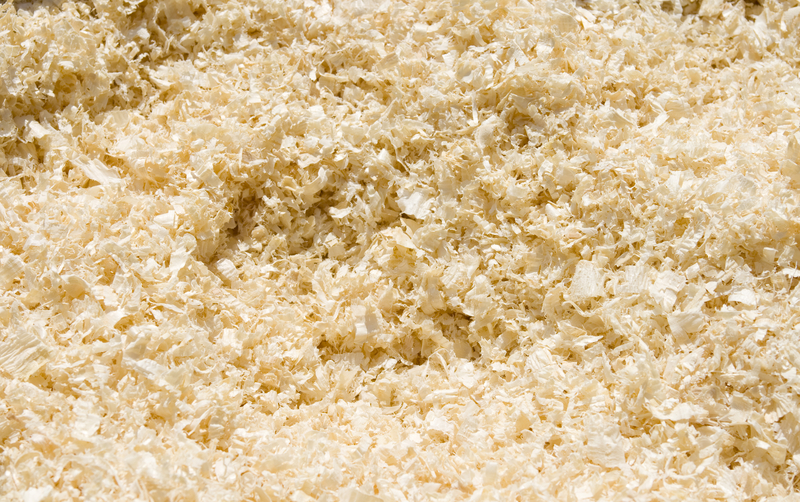
Researchers on the US Division of Vitality’s Oak Ridge Nationwide Laboratory (ORNL) and the College of Maine have unveiled a 3D-printed, recyclable, natural-material flooring cassette they are saying is powerful sufficient to interchange steel-and-concrete flooring in multi-storey buildings.
They mentioned the durability of the “SM2ART Nfloor cassette” comes from its mixture of polylactic acid (PLA) – a biodegradable thermoplastic derived from corn residue – and wooden flour comprised of lumber-processing waste.
“The PLA and wooden flour mix is a wonderful materials for producing recyclable, large-format additively manufactured elements,” mentioned Scott Tomlinson, structural engineer with the College of Maine’s Superior Buildings and Composites Heart (ASCC).
“This single-piece flooring meeting is stiffer and offers an improved strolling expertise when in comparison with the steel-concrete meeting it replaces,” he added.
ORNL researcher Katie Copenhaver mentioned: “By utilising bio-based, large-scale 3D printing, we changed an meeting comprised of 31 elements and three supplies with a single-material flooring panel that’s ecologically pleasant and with the identical power as conventional metal flooring fabrication.”
In April, the ASCC unveiled a thermoplastic polymer printer that broke world dimension data.
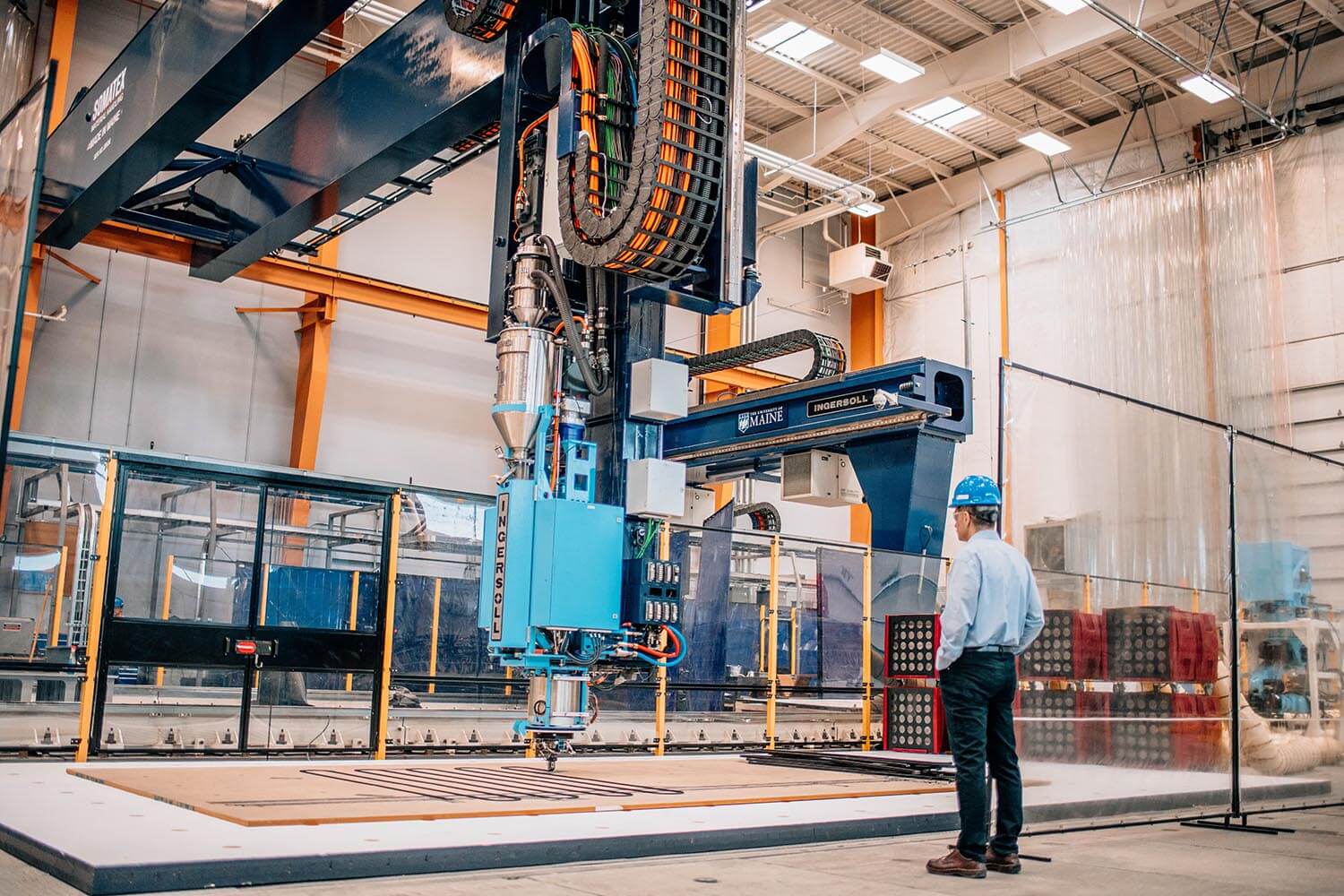
Dubbed the “Manufacturing facility of the Future 1.0”, it could print objects as much as 96ft-long, 32ft-wide, and 18ft-high.
The ASCC mentioned it may be used for reasonably priced housing, bridges, and wind farms.
The printer laid down layers for the geometrically-shaped cassette in about 30 hours, which researchers mentioned represented a labour saving of about 33% in comparison with constructing a conventional flooring.
It was programmed to go away openings for electrical, plumbing, and air flow providers.
Researchers mentioned a giant a part of the price of conventional flooring development comes from employees chopping such openings retrospectively.
“3D printing can save money and time by printing the ground cassette with cutouts designed into the completed product,” mentioned Copenhaver. “The one human labor entails putting in acoustic pores and skin for sound proofing and the resident’s desired flooring protecting.”
The cassette is absolutely recyclable, based on the researchers.
The thought for the mission got here from New York Metropolis-based SHoP Architects.
“They requested if we might mass-produce flooring panels extra effectively with greener supplies and additive manufacturing,” mentioned Copenhaver.
“Determining one thing new, contemplating completely different variables, is a trademark of ORNL. By means of experimentation, we labored out the correct speeds and made the tweaks wanted to reliably produce a completed half with the specified completed look and high quality.”
The Nfloor mission is a prototype. Analysis strikes now to flame retardants, insulation, and higher manufacturing methods.
UMaine’s Scott Tomlinson mentioned the know-how “holds plenty of promise for the way forward for sustainable buildings”.
- Subscribe right here to get tales about development around the globe in your inbox 3 times every week
Extra on various supplies: