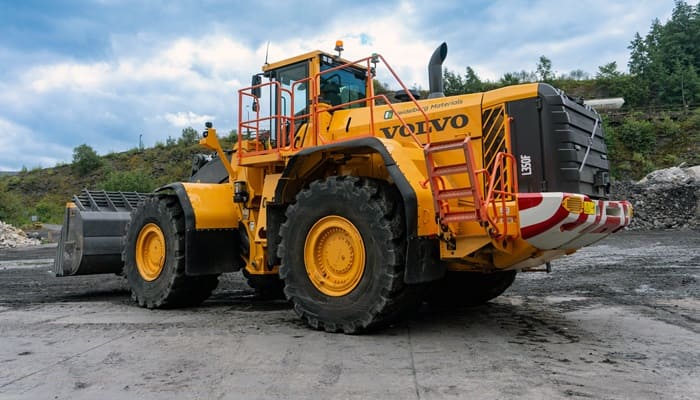
By extending the lifetime of a Volvo L350F wheeled loader, Heidelberg Supplies UK and SMT are demonstrating the facility of collaboration and the round economic system in decreasing carbon emissions and waste.
Heidelberg Supplies UK is without doubt one of the UK’s largest suppliers of constructing supplies, together with cement – a product liable for roughly 7% of all world CO2 emissions. Because of this, the corporate is keenly conscious of the environmental influence of its operations and has set bold targets to cut back emissions from its mixture, asphalt, concrete and cement manufacturing by 15% from a 2019 baseline by 2030, whereas additionally decreasing uncooked supplies consumption and waste.
Whereas the vast majority of Heidelberg Supplies UK’s emissions stem from the manufacturing of cement, a small but significant slice comes from the operation of its quarrying gear. Recognising this, the corporate has been scrutinising its fleet of heavy cell gear and crushers and planning the way it ought to evolve over the subsequent 5 years.
The best future fleet for Heidelberg Supplies UK would consist completely of zero-emission machines powered by electrical energy or hydrogen generated from renewable sources. Nonetheless, transitioning to those applied sciences requires the event of appreciable supporting infrastructures. As well as, most of the firm’s diesel machines are extremely sturdy and have years of service life remaining.
To bridge the hole, Heidelberg Supplies UK collaborated with Volvo seller SMT to refurbish an older wheeled loader. This avoids the acquisition of a brand new diesel machine that might run for a few years to return, in addition to the emissions and materials consumption related to its manufacture and transportation. Rebuilding older machines additionally provides sooner supply occasions and smoother operations as a result of current machine’s recognized historical past.
“Rebuilding current machines is a sustainable observe,” says Dominie Carver, a strategic account supervisor at SMT. “Rebuilds can lengthen machine life, recycle main elements and considerably cut back carbon emissions. Refurbishing a used engine for continued use, for instance, can save round 56% in CO₂ emissions, and a transmission of about 60%.”
To discover the potential of kit rebuilds, Heidelberg Supplies UK and SMT chosen a 14-year-old Volvo L350F wheeled loader used to load limestone into crushers on the Ribblesdale cement works in Clitheroe – one in all Heidelberg Supplies’ three UK vegetation producing Portland cement for numerous infrastructure initiatives. Regardless of the 21,341 working hours on the clock, the machine’s situation indicated that it might proceed to function reliably and productively with mandatory repairs and upgrades.
What the rebuild entailed…
The rebuild was carried out at SMT’s Newcastle depot, with lead engineer Michael Christer and expert welder Rhys Nixon assigned to supervise the mission from begin to end. The L350F was stripped again to the chassis, with new hydraulic pumps, hoses, steering techniques and refurbished cylinders put in to manufacturing facility requirements.
Vital work included the alternative of the driveline elements (entrance and rear axles, engine, transmission, dropbox and prop shafts) in addition to full line boring and restore of the load body and bucket, totally overhauled with a brand new specialised cutting-edge and strengthened put on plates for larger penetration and added safety. Upgrades to the machine to deliver it in keeping with fashionable Volvo requirements additionally included new lighting and high-intensity decals for higher visibility.
In the meantime, enhancements had been made to the cab for larger operator consolation, together with a refurbished seat, new ground mats, alternative headlining and an up to date switchgear. The Consolation Drive Management system was additionally put in to cut back operator pressure and stress.
“Regardless of the sheer measurement and energy of the L350F, it’s really easy to function,” says Andrew Graham, who operates the loader. “It’s identical to being in an armchair at residence.
“It’s bought nice visibility and, as a result of massive bucket measurement, we are able to cut back the variety of journeys to the crusher. This effectivity interprets to higher gasoline economic system and lowered tyre put on.”
The SMT rebuild course of sometimes takes round 12 weeks, with machines chosen primarily based on nationwide tips, service historical past, oil samples and part ageing. It additionally makes use of real Volvo elements, which means that the machine is roofed by a 24-month guarantee on main elements, providing Heidelberg Supplies UK peace of thoughts with no further prices for potential points.
Trying ahead to the long run
The collaboration between Heidelberg Supplies UK and SMT underscores the significance of sustainability and innovation within the building gear trade.
“Collaboration with suppliers comparable to SMT is essential for reaching Heidelberg Supplies UK’s sustainability targets,” says Elliot Wellbelove, carbon innovation supervisor at Heidelberg Supplies UK. “We are able to depend on SMT to supply emissions discount information for rebuilt machines, which is crucial for calculating environmental advantages and integrating them into our information techniques.”
The profitable rebuild of the L350F is a testomony to the strides Heidelberg Supplies UK and SMT are making in direction of decarbonisation, larger circularity, and improved operational effectivity – and Heidelberg Supplies UK now plans to increase the rebuild programme to different websites throughout the UK. The partnership with SMT can also be anticipated to broaden, specializing in improvements comparable to electrification and hydrogen-powered equipment.
“Now we have been a Volvo and SMT buyer for a very long time,” says Luke Morgan, Heidelberg Supplies’ UK fleet supervisor. “The SMT relationship has developed fairly considerably over the previous few years.
“We respect the professionalism of a structured method in direction of the rebuilding of the machines and within the wider approach during which SMT operates. Our confidence within the success of the rebuild was because of expertise of SMT’s experience and approach of working.”
This regeneration effort promotes a wholesome round economic system and is an important step within the transition towards a carbon-free trade. It additionally exemplifies how strategic collaboration and technological developments can result in impactful environmental advantages, with out compromising productiveness or high quality.