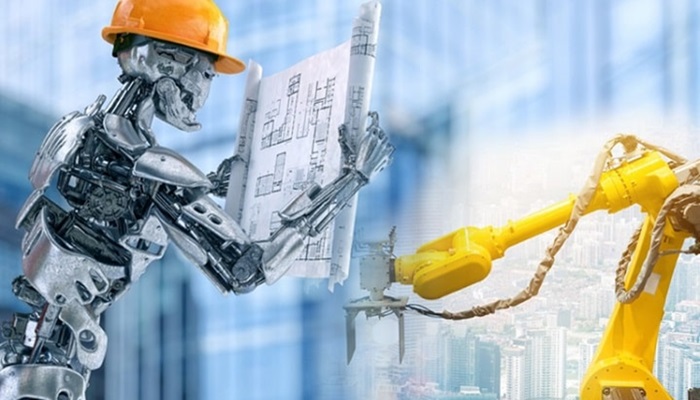
The development business stands at a essential crossroads. Whereas demand for building initiatives continues to surge throughout residential, business and infrastructure sectors, the business faces a persistent problem threatening its development: a extreme scarcity of expert staff, particularly in constructing supplies manufacturing. In line with the Bureau of Labor Statistics, building job openings remained stubbornly excessive at 338,000 as of April 2023, highlighting a talented labor disaster that reverberates all through the development provide chain.
The Evolution of Workforce Challenges in Manufacturing
The influence of this workforce scarcity creates a cascading impact all through the development provide chain. When constructing supplies producers battle to keep up optimum manufacturing ranges attributable to staffing challenges, building initiatives face delays, prices enhance and the broader economic system feels the pressure. The scenario has change into notably acute as skilled staff retire, taking many years of useful information with them, whereas fewer younger folks enter the business.
Abilities growth on this context transcends mere coaching. It requires cultivating a complete set of competencies together with problem-solving, essential considering, creativity, and adaptableness, whereas fostering a tradition of steady studying. Conventional strategies of monitoring worker abilities and managing workforce growth via spreadsheets are now not ample, particularly as manufacturing environments change into extra autonomous and frontline staff tackle larger accountability.
Harnessing AI and Information to Remodel Employee Growth
In line with the McKinsey International Institute, manufacturing is the only most data-prolific business, producing an astonishing 1.9 petabytes of knowledge yearly. But producers are solely starting to faucet into how AI can leverage that knowledge to upskill, prepare, help and have interaction frontline workforces. Fairly than viewing the workforce problem solely as a hiring drawback, forward-thinking business leaders are utilizing this knowledge to revolutionize how they help and develop their frontline workforce.
AI implementation in manufacturing isn’t about changing staff or including synthetic intelligence as an afterthought to current techniques. As a substitute, it serves as the inspiration for augmenting staff and creating an adaptive, responsive method to constructing capabilities in industrial workforces. AI-powered platforms that embody generative AI assistants, copilots, and brokers can act on this workforce knowledge and supply personalised, real-time steering tailor-made to particular person wants and speed up talent acquisition thereby decreasing time-to-competency. These techniques can perform as “digital coaches,” accessible each time staff want help throughout their workflow processes. This method is especially essential in semi-structured processes the place staff have to adapt to variable circumstances whereas sustaining high quality and security requirements.
Constructing a Sustainable Future for Manufacturing
The way forward for constructing supplies manufacturing relies on operationalizing studying—integrating coaching into day by day operations and emphasizing a scientific strategy of buying new abilities. AI-enabled techniques help this by offering real-time steering, capturing and sharing tribal information, and enabling focused workforce growth initiatives. Methods that incorporate generative AI brokers can streamline the seize and digitization of essential tribal information from senior, extra skilled staff. These generative AI brokers can then rework that captured tribal information into personalised work directions and steering for less-experienced staff, providing a direct answer to closing the talents hole. These platforms create a steady loop between required abilities endorsements and precise work efficiency, enabling producers to determine each excessive performers and those that want further help.
Firms implementing these options report quicker onboarding, fewer skilled callouts, and constant closures of talent gaps throughout their workforces. The expertise not solely helps tackle rapid staffing challenges but additionally creates extra partaking and satisfying work environments that assist appeal to and retain expertise. Sensible related workforce expertise permits consultants to information trainees via robust duties remotely, whereas frontline staff can entry commonplace procedures and processes through AI assistants, view micro-targeted content material, and get skilled directions immediately on the store ground.
Conclusion
The expert labor scarcity in building and constructing supplies manufacturing presents a big problem, but additionally a chance to reimagine how we help and develop our workforce. In contrast to fears of obsolescence in lots of white-collar jobs, AI is augmenting the talents of frontline staff whereas leveraging producers’ knowledge to assist personnel change into extra productive, engaged and happy of their roles.
As employee churn charges proceed to rise and conventional coaching strategies show inadequate, AI-enabled related employee options have advanced from a “nice-to-have” to a essential device for sustaining security, productiveness and high quality in trendy manufacturing environments. The trail ahead isn’t about selecting between human staff and expertise—it’s about discovering modern methods to mix the 2, guaranteeing that producers have the instruments, coaching, and help wanted for fulfillment in an more and more advanced industrial panorama.