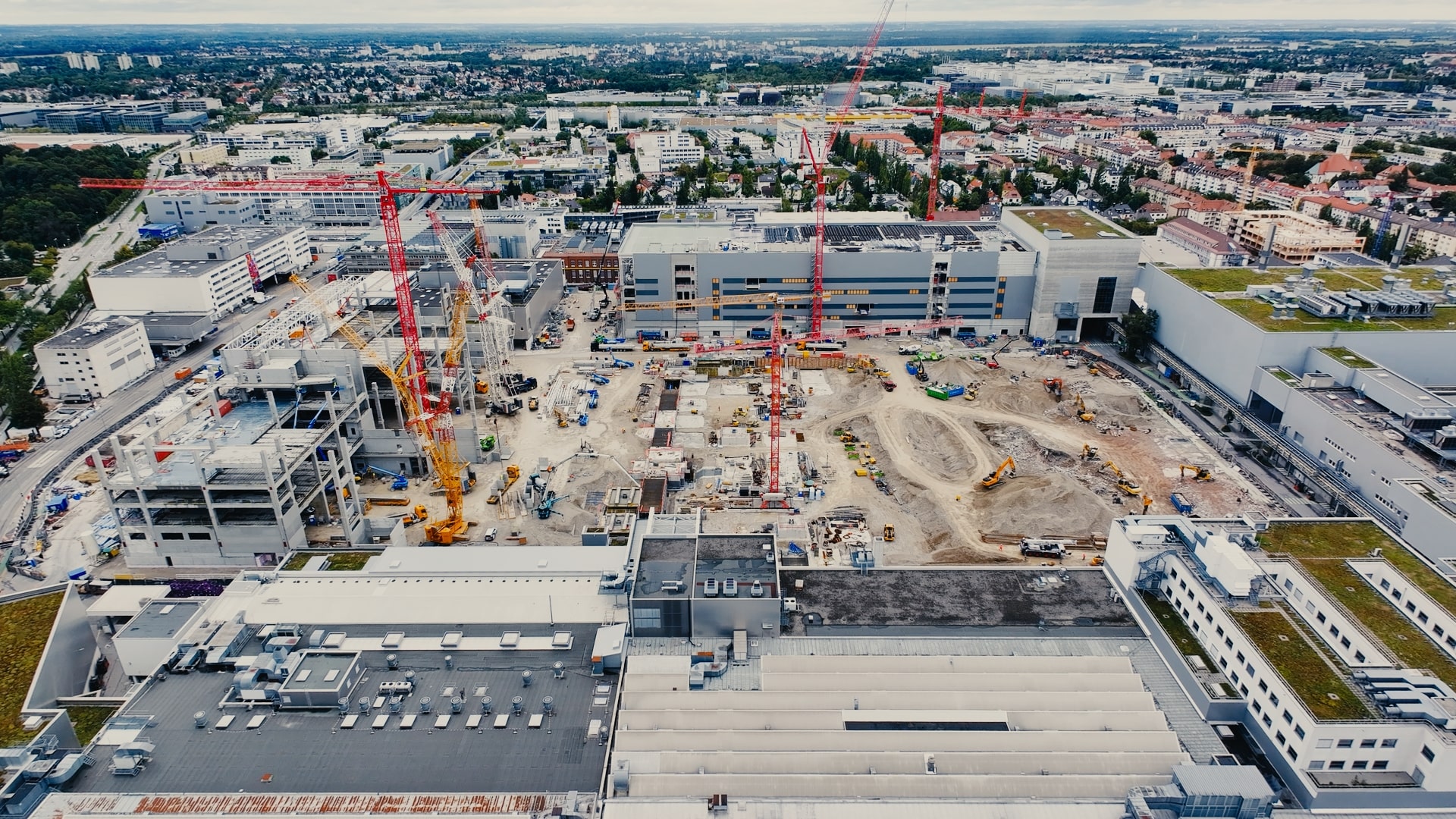
German advisor Drees & Sommer has described how it’s steering a €650m conversion of BMW’s essential manufacturing unit in Munich to arrange it for producing vehicles with electric-only drive techniques from 2026.
It’s utilizing a type of partnering in addition to “lean” building rules and a digital twin to ship new manufacturing halls with out disrupting operations on the website, the place practically 7,000 workers produce a thousand automobiles a day.
Drees & Sommer is working with German contractor and engineer Porr on the undertaking.
“The largest building problem is the tight schedule,” stated Drees & Sommer’s senior workforce head, Maximilian Lammel
“We began the demolition work in April 2023 – the brand new automobiles should roll off the manufacturing line in November 2026. Throughout this era, the development work should not intervene with ongoing automobile manufacturing. For this to work, an environment friendly building workflow is essential.”
The undertaking makes use of a supply technique often called “common contracting in partnering” wherein the consumer, undertaking supervisor, and building agency work together as companions in all phases.
“Mutual and joint duty improves the communication between stakeholders and enhances the standard of building initiatives,“ says Maximilian Lammel.
“In standard supply strategies there are various sub-areas of duty, with communication being performed through a number of interfaces. This usually results in misunderstandings and hampers the circulation of knowledge, particularly in large-scale initiatives. The implications could possibly be disastrous.”
The workforce is making use of “lean” manufacturing rules borrowed from the automotive business itself.
One lean precept is the exact timing of every step in manufacturing. If timing slips, supervisors discover and repair the fault immediately.
“On a standard constructing website, however, defects usually go unnoticed for a very long time – typically so lengthy that, in some unspecified time in the future, all work involves a standstill,” Drees & Sommer famous.
The corporate’s automotive division head Florian Langlotz stated the undertaking’s programme was developed “in as a lot element as needed, so that each one trades work collectively to the very best impact”.
That led to a transparent definition of which workers, machines, supplies have been wanted at a given place and time.
“To keep away from any nasty surprises on the constructing website, we use digital planning,” stated Drees & Sommer’s senior workforce head Simon Rogalski.
“Every constructing is initially deliberate within the type of a digital twin, which brings collectively all of the related information. On this technique, the development planners not solely describe the geometry of the brand new halls. The mannequin could be enhanced with completely different varieties of information on the supplies used, their price and repair life, in addition to sound insulation and hearth security properties.”
All events within the undertaking use the identical mannequin, so any battle within the mannequin exhibits up immediately.
“Errors usually are not left unnoticed till the development course of, the place they might then result in costly delays,” the corporate stated.
This stage of planning does improve the planning effort at the beginning, however pays off over the course of the undertaking, it added.
- Subscribe right here to get tales about building around the globe in your inbox thrice every week