Tasks are all about delivering a services or products. Whether or not you’re working in mission administration, manufacturing, provide chains or stock administration, it is advisable to ship one thing precious to your prospects. That is why lead time is so essential.
There are various phases between the preliminary concept and the completed product, and understanding your lead time allows you to ship well timed tasks. Let’s take a second to outline lead time, decide find out how to calculate it and see the way it works throughout numerous industries.
What Is Lead Time in Manufacturing?
Lead time is a producing key efficiency indicator (KPI) the interval between the beginning of a course of and its conclusion. For instance, this may very well be the period of time it takes to make a product from scratch, the time it takes to course of buy orders or the wait time that spans between the product being shipped and the shopper receiving it. Lead time is utilized in numerous industries from manufacturing to provide chain administration and mission administration.
The typical lead time differs throughout industries. Although there could also be similarities, the lead time modifications based mostly on numerous processes. One factor that each one industries have in widespread is that lead time permits companies to schedule work and provides their purchasers or end-users a deadline by which they’ll obtain the product. One other method that lead instances could be useful is by evaluating the outcomes of your preprocessing, processing and postprocessing phases to find inefficiencies that you could weed out in future tasks to work extra productively.
To higher handle your lead time, you possibly can depend on mission administration software program. ProjectManager is mission administration software program that helps you observe work in actual time. One of many a number of mission views is the kanban board that lets you observe numerous manufacturing processes, make a plan and collaborate along with your workforce in actual time. Get began with ProjectManager right this moment without spending a dime.
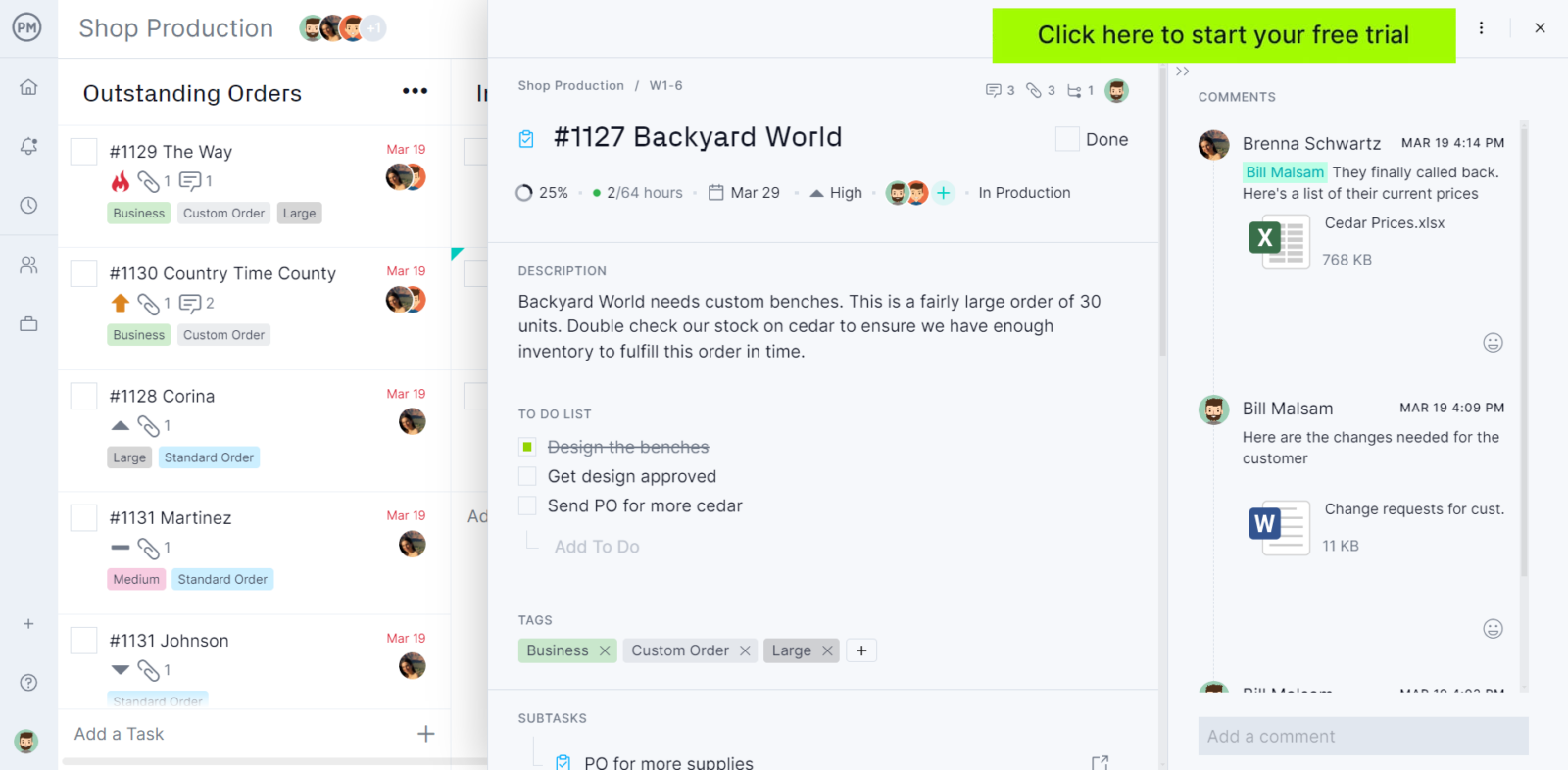
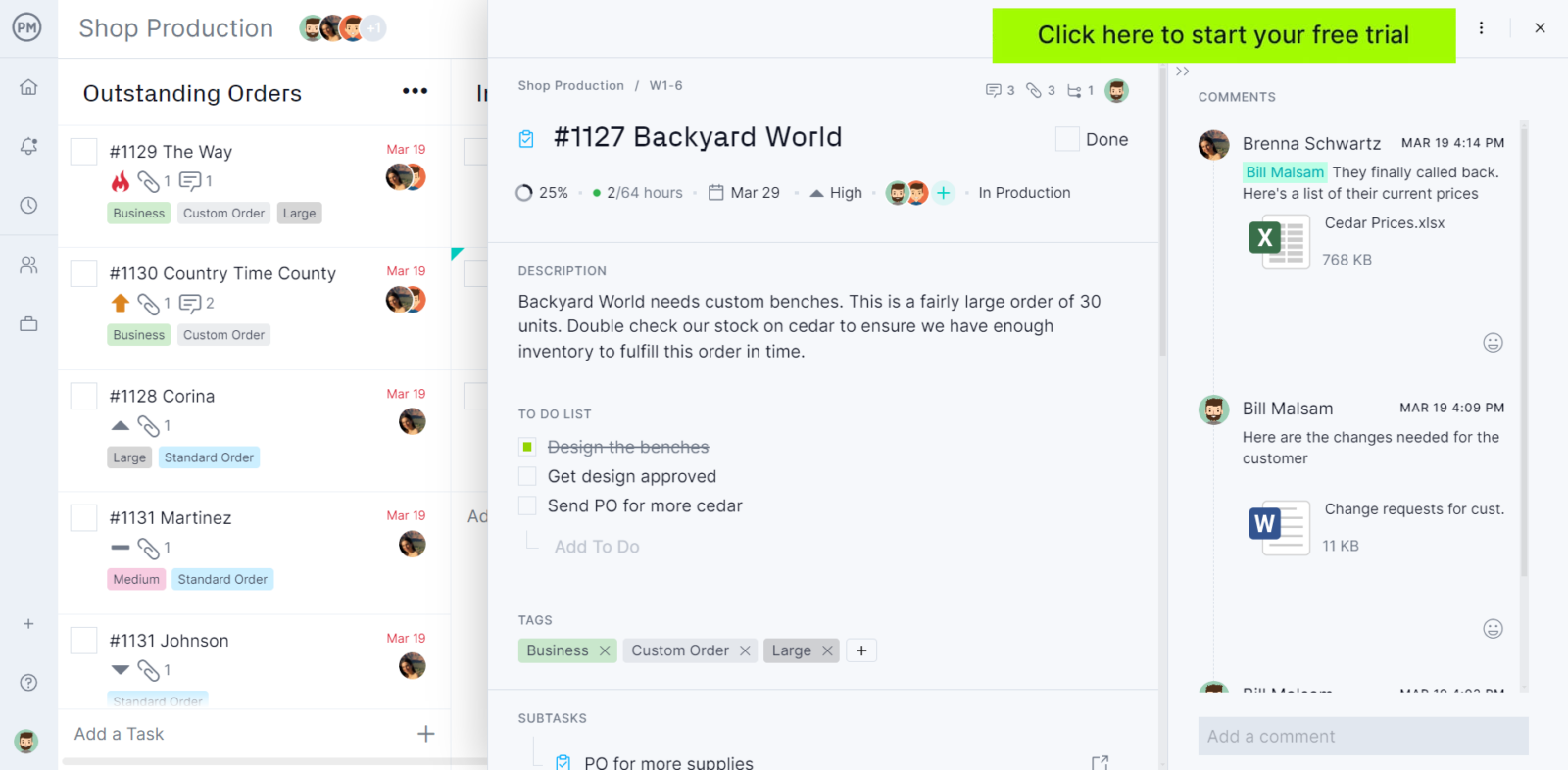
Elements of Lead Time
The parts of lead time are usually not set in stone as they will differ from one business to the subsequent. Usually, listed here are the six parts of lead time.
- Pre-processing lead time can also be known as planning time. It speaks to the time it takes to obtain a request for replenishment or the event of a mission. It takes time to grasp the request and create a purchase order order in the event you’re shopping for one thing or making a job.
- Processing lead time happens after receiving the acquisition order and refers back to the time it takes to acquire or produce the merchandise.
- Submit-processing lead time is a mixture of the lead instances of all of the processes that happen after merchandise have been manufactured, together with storage, transportation and inspection lead instances.
- Ready time is the interval between procuring the required assets and the time when merchandise manufacturing takes place.
- Storage time refers to stock or the time your completed product is within the warehouse or manufacturing facility earlier than it will get delivered.
- Transportation time is the time it takes to maneuver the product from the warehouse or manufacturing facility to the shopper.
- Inspection time is the time it takes for the product to be appeared over and permitted by the shopper after it’s delivered. This would possibly require some forwards and backwards to cope with any points with the merchandise.
Find out how to Calculate Lead Time
Now that we perceive the definition and parts of lead time from order to supply, how do you calculate lead time? This essential metric is likely one of the easiest calculations you’ll discover when managing a mission, provide chain or manufacturing course of.
Correct lead time calculations enable you order the correct amount of uncooked supplies to your warehouse, a pricey course of that may take up precious actual property in the event you order an excessive amount of. On the flip aspect, you additionally wish to have sufficient inventory available to satisfy your orders. That stability of stock is why calculating lead time is important.
There are some phrases to grasp when calculating lead time comparable to provide delay and reordering delay. Provide delay is how lengthy your provider takes to satisfy a buyer order after it’s positioned. A reordering delay is the time between the fulfilled order and the location of the subsequent order.
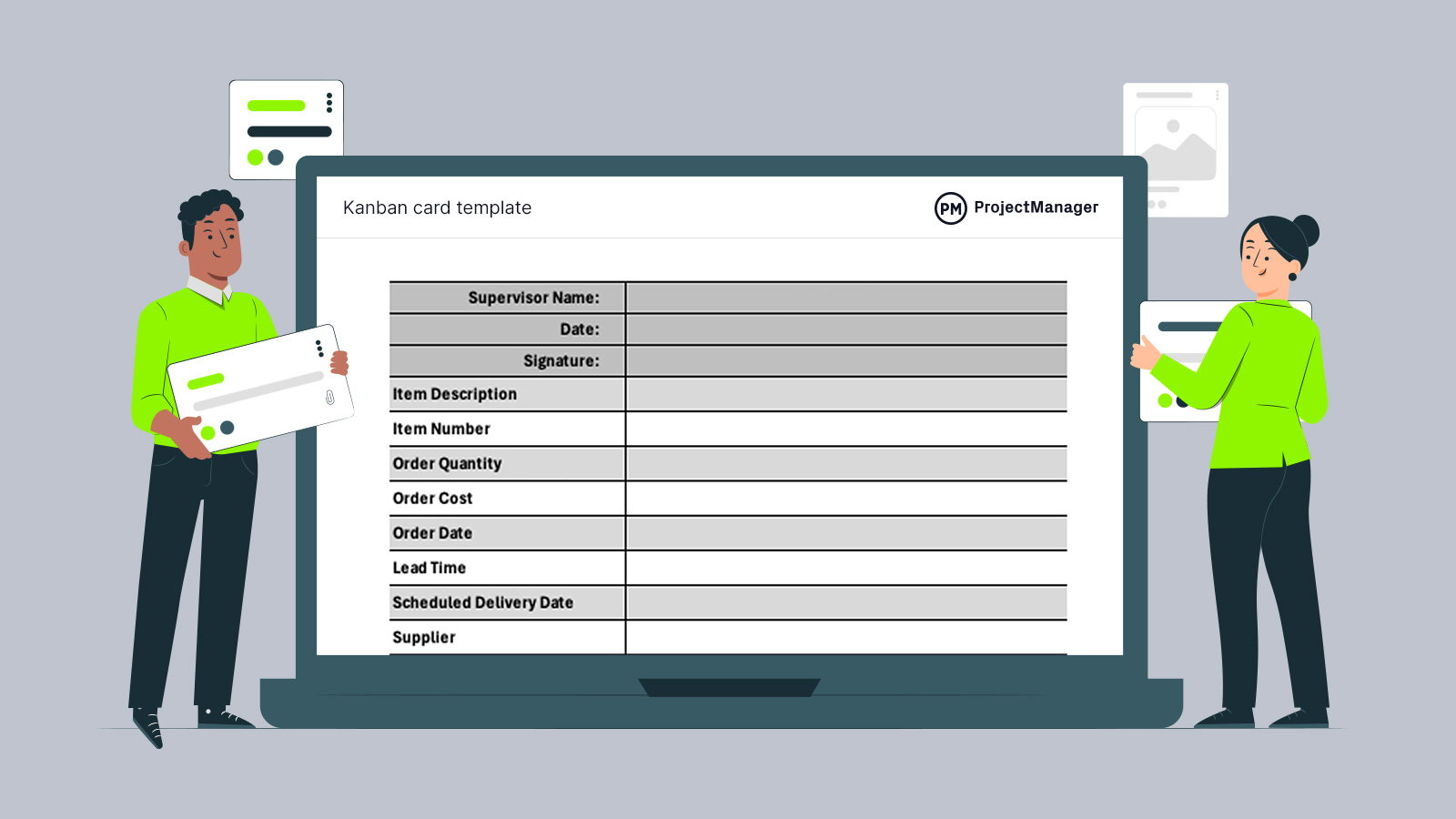
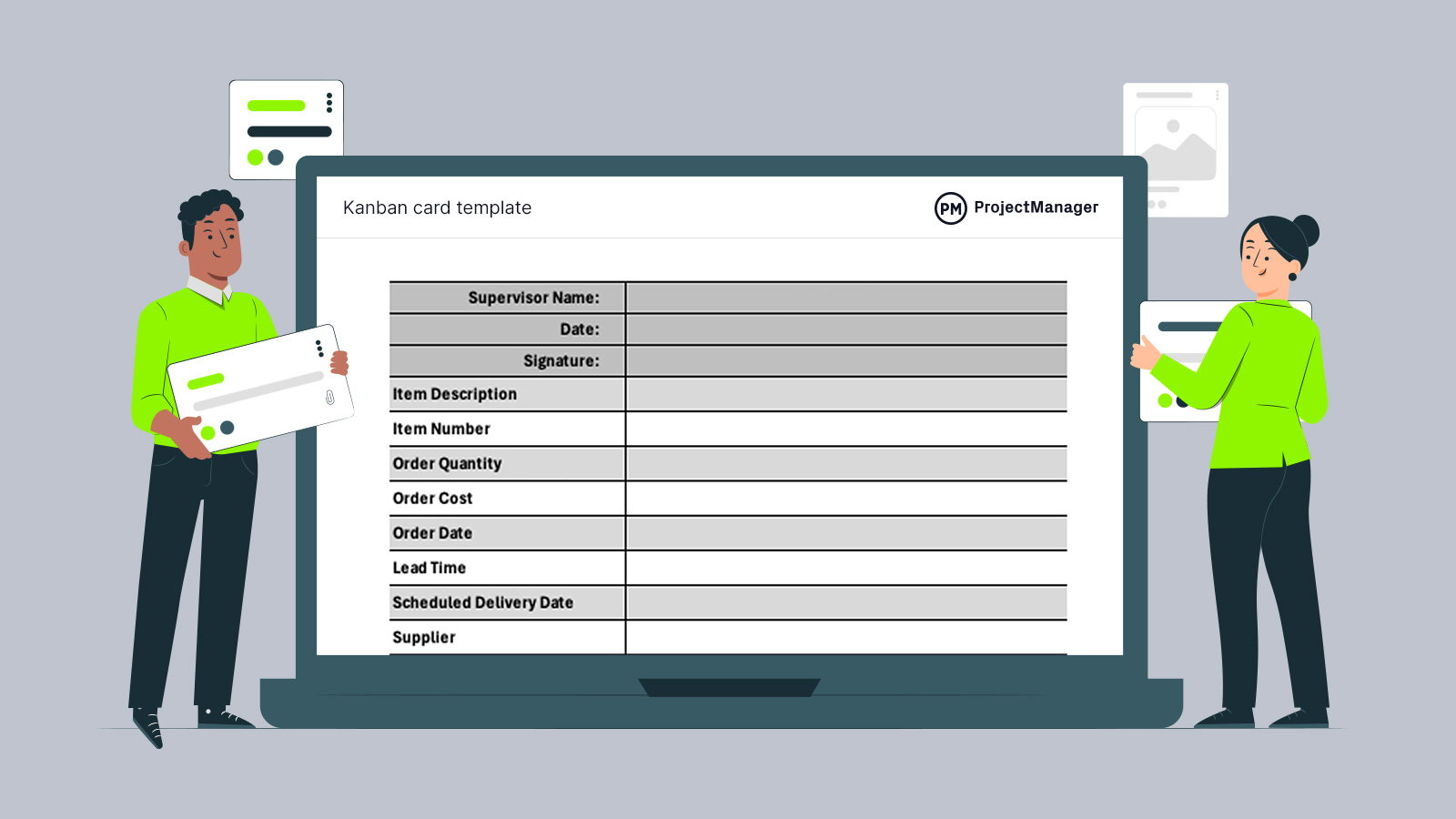
Get your free
Kanban Board Template
Use this free Kanban Board Template for Excel to handle your tasks higher.
Lead Time Method
There isn’t one strategy to calculate lead time, however the commonest is to subtract the order request date from the order supply date. This is called the order lead time system.
Lead Time (LT) = Order Supply Date – Order Request Date
Nonetheless, the order lead time system solely provides a common overview of the length of a producing course of, which leads some mission managers to make use of the manufacturing lead time system under to get a extra detailed view of the steps that happen between the second a buyer locations the order and he receives it.
Lead Time = Pre-Processing Time + Processing Time + Submit-Processing Time
These lead time parts could be additional divided into order, manufacturing, manufacturing and supply lead instances. We’ll zoom into every of those in a while on this information.
Manufacturing Lead Time Instance
To higher perceive the idea of lead time, let’s have a look at an instance. Take manufacturing, Acme Manufacturing wants to supply 750 widgets to fulfill its manufacturing finances. With its present manufacturing fee, it’s going to produce 25 widgets a day. On this case, lead time = works in progress/common manufacturing fee. Due to this fact, the lead time for this instance is 30 days. There could be fluctuations within the work-in-progress completion time, however this supplies a common concept of Acme Manufacturing’s lead time.
Kanban Board Template
Kanban boards are a job administration software that can be utilized to calculate the lead time of any kind of workflow. They encompass two important components, kanban columns and playing cards. Columns mirror phases of a course of, whereas kanban playing cards maintain details about duties comparable to an outline, their begin and finish dates, precedence stage, subtasks, and extra. These playing cards are moved all through the columns to point out the stage of completion of duties. For instance, kanban boards can be utilized to handle the method of producing a product and calculate the lead time of manufacturing actions.
This free kanban board template for Excel could be simply personalized by modifying the cells that make up the kanban boards and kanban playing cards. By default, it’s going to assist you to observe the beginning and finish dates of duties, however you possibly can add as many job particulars as needed by including further rows to the kanban playing cards. Merely observe the steps on our template web page to get began.
Lead Time vs. Cycle Time
Cycle time and lead time are each metrics used to judge the effectivity and responsiveness of processes. Nonetheless, they’ve completely different scopes and focuses. Cycle time is the time it takes to finish a job from the purpose at which it begins to the purpose at which it’s completed. Cycle time focuses on the energetic work course of, comparable to coding, reviewing and deployment.
As famous above, lead time is the time it takes to ship a services or products to a buyer, from the purpose the shopper requests the purpose at which they obtain the services or products. Due to this fact, lead time contains the whole workflow, together with any wait instances or delays.
Varieties of Lead Time in Manufacturing
The time period lead time refers to barely various things in manufacturing in addition to measuring the time it takes to supply a product. The idea of lead time additionally applies to different manufacturing processes comparable to managing inventories, operational tasks, order success or transport and supply.
Manufacturing Lead Time
Manufacturing lead time is a selected kind of lead time in manufacturing, which measures how lengthy it takes to course of, put together supplies, manufacture and ship your order. To calculate this metric, you’d add preprocessing, processing and post-processing knowledge to get your lead time.
Manufacturing lead time is made up of fabric lead time, which is the time it takes to ship supplies to the producer. In manufacturing administration, lead time is how lengthy it takes from the purpose of getting supplies to producing a completed product. Buyer lead time is the interval of transferring the completed merchandise from the producer to the shopper.
Lead Time in Stock Administration
Lead time in stock administration is how lengthy it takes to restock between the time of the order to when it’s acquired. This impacts how a lot stock an organization must warehouse to take care of the manufacturing cycle they’ve determined upon. Discovering this lead time in stock administration requires including the availability delay with the reordering delay. It’s all the time excellent to all the time have sufficient provide on demand to feed the manufacturing course of and preserve the manufacturing flowing.
That is barely completely different than in manufacturing, nevertheless, as a result of it doesn’t embody processing stock or uncooked supplies into the ultimate product. In manufacturing, you will need to additionally think about the supply of the product to the shopper or retailer.
When coping with stock administration, you’ll embody the availability delay and the reordering delay. To calculate lead time on this occasion, add the availability delay to the reordering delay.
Lead Time (LT) = Provide Delay (SD) + Reordering Delay (RD)
Lead Time in Provide Chain Administration
Just like manufacturing, the availability chain lead time is the size of time it takes from producing a purchase order order to delivering that merchandise. And as in manufacturing, every a part of that offer chain lead time has its personal lead time:
- Materials lead time is the time it takes for uncooked supplies to be delivered to the manufacturing facility.
- Manufacturing lead time is how lengthy it takes the manufacturing facility to get an order by manufacturing and ship the completed items.
- Buyer lead time is the time when a buyer makes an order to after they obtain that order.
Including these lead instances collectively offers you the overall lead time. Nonetheless, with regards to satisfaction, crucial lead time is how lengthy it takes to achieve the shopper. As prospects have come to anticipate quick supply instances, in the event you can shorten buyer lead time, you possibly can enhance gross sales.
Order Lead Time
Order lead time is how lengthy it takes to course of an order. This is applicable to lots of the industries listed above. Extra particularly, it’s the minimal period of time between the acquisition order and supply of the product.
To determine the order lead time, it is advisable to know the next:
- Precise order lead time (A-OLT) is how lengthy it takes from getting the order to fulfilling it.
- Requested order lead time (R-OLT) is the time between the order and when the shopper needs supply.
- Quote order lead time (Q-OLT) is the time between the order entry date and supply date as it’s represented on the contract.
- Confirmed order lead time (C-OLT) is the date on which the supply has been confirmed.
Supply Lead Time
Supply lead time is the period of time it takes for a product to journey from a provider to a buyer. It’s a key metric in provide chain administration. Supply lead time is calculated by including up manufacturing time, processing time and transportation time.
Lead Time in Undertaking Administration
Lead time in mission administration happens when one exercise begins as one other is being executed. It’s additionally known as working in parallel. Lead time also can discuss with job dependencies, comparable to finish-to-start relationships, the place one job should be full earlier than the subsequent can start. That is completely different than lag time in mission administration, which is the period of time that should move earlier than one other job can start. Lag can also be a part of job dependencies and it could possibly happen in all 4 job dependencies: finish-to-start, start-to-start, finish-to-finish and start-to-finish.
Nonetheless, each lead and lag time are used when making a mission schedule. It helps mission managers sequence their actions and duties to fulfill the mission deadline. A simple strategy to bear in mind these phrases is that lag is holding up time and lead is hurrying up time.
Find out how to Cut back Lead Time
There are a number of methods to scale back lead time. Listed below are a few of them.
Map Enterprise Processes and Optimize Workflows
Mapping enterprise processes and optimizing workflows might help scale back lead time by figuring out bottlenecks and redundancies in addition to streamlining execution strategies. Utilizing a workflow diagram might help visualize the processes and assist determine strengths and weaknesses in it.
Steadiness Your Staff’s Workload
Balancing the workforce’s workload retains them working at capability, which results in higher productiveness. Apart from ensuring assets are distributed evenly, managers can prioritize duties, delegate work and talk extra successfully.
Enhance Useful resource Capability
There are a number of methods to scale back lead time by rising useful resource capability. Demand forecasting makes use of historic knowledge to find out the demand for a services or products, which helps ship it when a buyer wants it. Collaborating with suppliers lets them know when to anticipate reorders based mostly on gross sales knowledge, which permits them to hurry up the success course of. Automating duties and optimizing manufacturing scheduling also can scale back lead time.
How ProjectManager Helps With Lead Time Discount
No matter which business you’re employed in, ProjectManager is a perfect software to trace your lead time and overcome inefficiencies. Our software program delivers real-time knowledge that helps you discover points that may delay your manufacturing and repair them quick to remain productive.
Monitor Progress and Efficiency on Actual-Time Dashboards
Our real-time dashboards mechanically seize and calculate reside knowledge earlier than displaying it on colourful graphs that observe time, prices and 4 different metrics. You get a high-level view of your manufacturing to catch anomalies and resolve them earlier than they will trigger issues. There’s no setup as with inferior software program merchandise and it’s prepared to make use of if you end up.
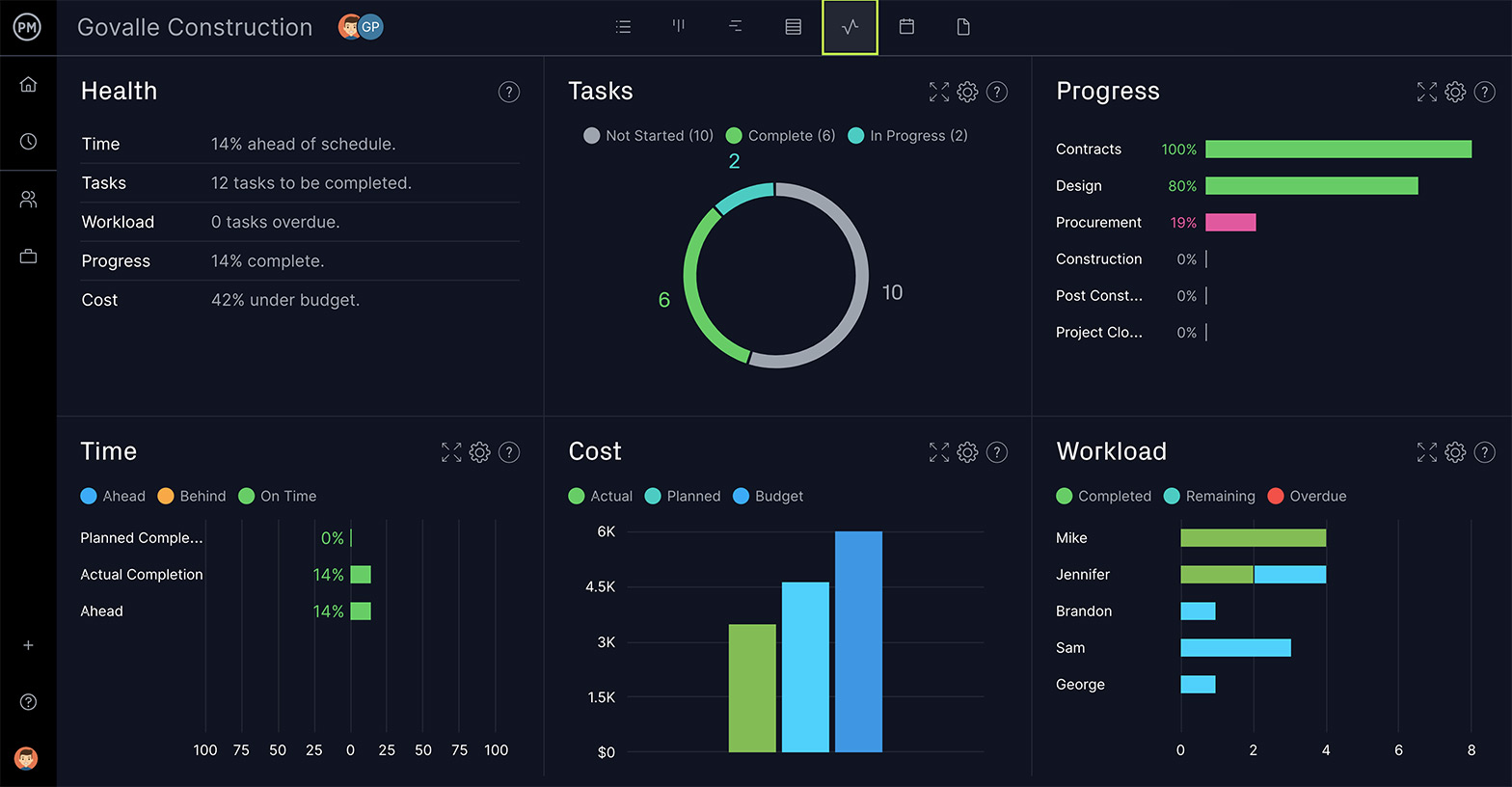
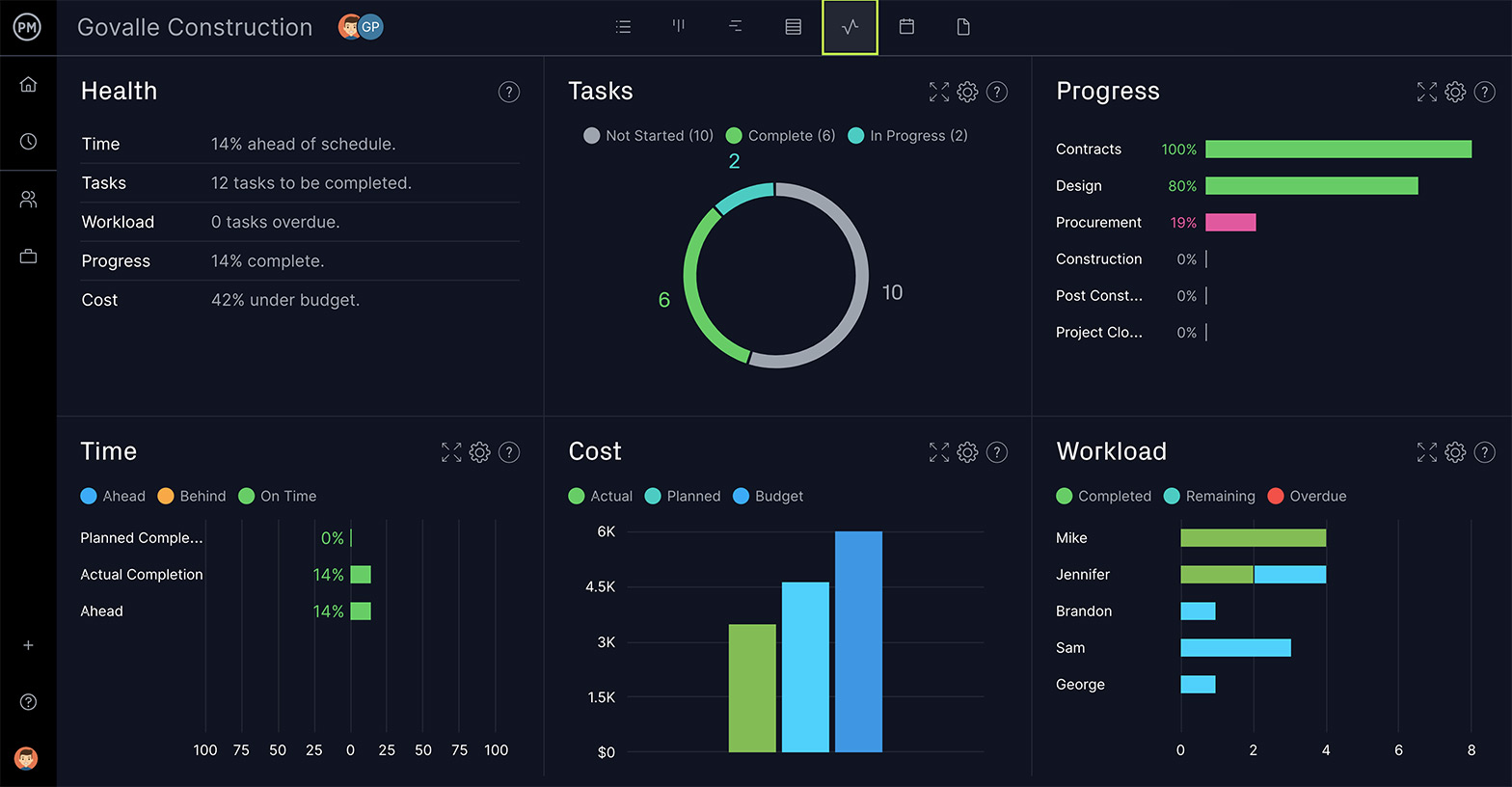
Dive Deeper Into Knowledge With Sturdy Reporting Options
The extra knowledge, the higher. With a keystroke, you possibly can dive into mission standing, portfolio standing, workload, prices, duties and a lot extra. Each report could be filtered that will help you zero in on what you’re in search of. The stories are additionally straightforward to share as a PDF attachment and even print out to maintain stakeholders up to date on progress.
You’ve seen how our Gantt chart helps you intend, whereas dashboards and stories feed you the info it is advisable to keep on schedule and inside your finances. There are additionally useful resource administration options that assist stability your workload and preserve your groups working at capability to fulfill your lead time each time.
ProjectManager is award-winning software program that connects hybrid groups and helps everybody work collectively and productively. Arrange duties, groups and tasks with a collaborative platform that connects everybody in actual time. Be a part of groups at NASA, Siemens and Nestle who use our software program. Get began with ProjectManager right this moment without spending a dime!